Ingenious Cane Sugar Processing Chemicals: Optimize Your Process
Wiki Article
Maximizar Rendimientos Y Minimizar Costos: Estrategias Avanzadas Para La Optimización Química Del Procesamiento De Azúcar De Caña
In the world of walking cane sugar processing, the pursuit of making the most of yields while concurrently lessening prices stands as an awesome difficulty that requires a critical mix of advanced chemical optimization methods. The complexities of this venture dig into the core of performance, where every component of the process plays an important function in accomplishing optimal end results. By checking out the complexities of chemical analysis, enzyme use, pH control, filtering, and purification techniques, a landscape abundant with possibilities for enhancement and development arises. Amidst this intricate internet of approaches exists the guarantee of unlocking untapped capacity and reinventing the extremely significance of sugar manufacturing. Cane Sugar Processing Chemicals.Chemical Analysis for Effectiveness
Chemical analysis plays an essential duty in enhancing the effectiveness of sugar walking cane processing by offering essential understandings right into the structure and properties of the raw products. By conducting thorough chemical evaluations on sugar walking cane examples, processors can establish the exact concentrations of sucrose, sugar, fructose, and various other parts existing in the raw material. This details is vital for maximizing the different stages of the sugar cane handling chain, from grating to condensation.In addition, chemical analysis enables cpus to recognize contaminations such as organic acids, proteins, and minerals that can influence the quality and return of the final sugar item. By quantifying these contaminations, processors can implement targeted approaches to get rid of or alleviate their effects, inevitably enhancing the total effectiveness of the processing plant.
Furthermore, chemical analysis facilitates the monitoring of procedure parameters such as pH, temperature, and viscosity, allowing processors to make real-time adjustments to ensure optimum problems for sugar extraction and crystallization. On the whole, a thorough understanding of the chemical make-up of sugar cane is crucial for taking full advantage of returns, minimizing expenses, and preserving high product high quality in the sugar manufacturing market.
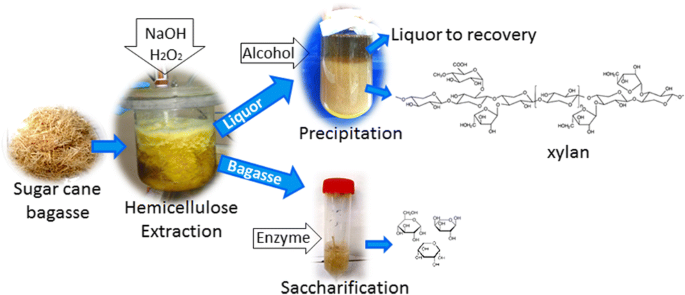
Enzyme Usage for Enhanced Returns
With a critical method to enzyme utilization, sugar cane processors can substantially boost their yields while preserving functional efficiency in the production process. Enzymes play a critical duty in sugar cane processing by breaking down complicated carbs right into less complex sugars, thus enhancing the total sugar extraction performance. By integrating certain enzymes tailored to target the different parts of sugar cane, such as cellulose and hemicellulose, processors can boost the launch of sugars during removal.Enzyme utilization uses the advantage of maximizing sugar yields from the raw product while lessening the power and resources needed for processing. This results in an extra lasting and economical manufacturing process. Additionally, enzymes can help in decreasing processing time and improving the overall top quality of the sugar product. Through careful selection and application of enzymes, sugar cane processors can optimize their procedures to attain higher returns and productivity.
Ph Control for Optimum Handling
Enzyme application for raised yields in sugar walking cane processing lays the structure for attending to the essential element of pH control for optimal handling effectiveness. Maintaining the ideal pH level throughout various stages of sugar walking cane processing is important for optimizing yields and reducing expenses. pH control is especially critical during the extraction and explanation processes. In the removal stage, preserving the proper pH assists in attaining efficient sucrose extraction from the cane. Controlling the pH throughout clarification aids in the precipitation of contaminations and non-sucrose components, bring about a purer end product. In addition, pH influences the activity of enzymes included in the break down of macromolecules, affecting the general effectiveness of the procedure. By very carefully keeping an eye on and adjusting the pH degrees at various handling steps, sugar walking stick cpus can improve sugar recuperation rates, decrease chemical usage, and enhance the total production procedure. Efficient pH control not only boosts the top quality of the end product yet additionally adds to sustainable and cost-efficient sugar walking stick handling procedures.Advanced Filtration Methods
Executing innovative filtering techniques in sugar cane handling enhances the effectiveness and pureness of the end product with improved splitting up approaches. By including innovative filtering modern technologies, such as membrane purification and activated carbon purification, sugar walking stick processing plants can accomplish greater levels of sugar healing and improved top quality control.
Activated carbon purification is one more sophisticated method that helps in the removal of colorants, off-flavors, and recurring impurities from sugar walking stick products. By making use of turned on carbon's adsorption buildings, this filtration technique improves the clearness and taste of the sugar, satisfying the high criteria required by customers and market guidelines.
Energy-Efficient Distillation Methods
Energy-efficient purification approaches are crucial for optimizing the sugar walking cane handling market's power consumption while maintaining top quality item criteria. Traditional distillation processes can be energy-intensive, resulting in greater manufacturing expenses and environmental effects (Cane Sugar Processing Chemicals). Applying energy-efficient purification approaches, such as vacuum purification or molecular distillation, can significantly minimize power demands while boosting total procedure performanceVacuum cleaner purification entails lowering the pressure within the distillation system, which decreases the boiling point of the liquid blend being refined. This reduction in boiling factor lowers the power required for vaporization, leading to energy financial savings compared to conventional purification methods.
On the various other hand, molecular distillation utilizes brief path purification strategies under high vacuum conditions to separate substances based upon their molecular weight. This technique is specifically effective for heat-sensitive materials, as it runs at reduced temperatures, decreasing energy intake and maintaining product quality.
Verdict
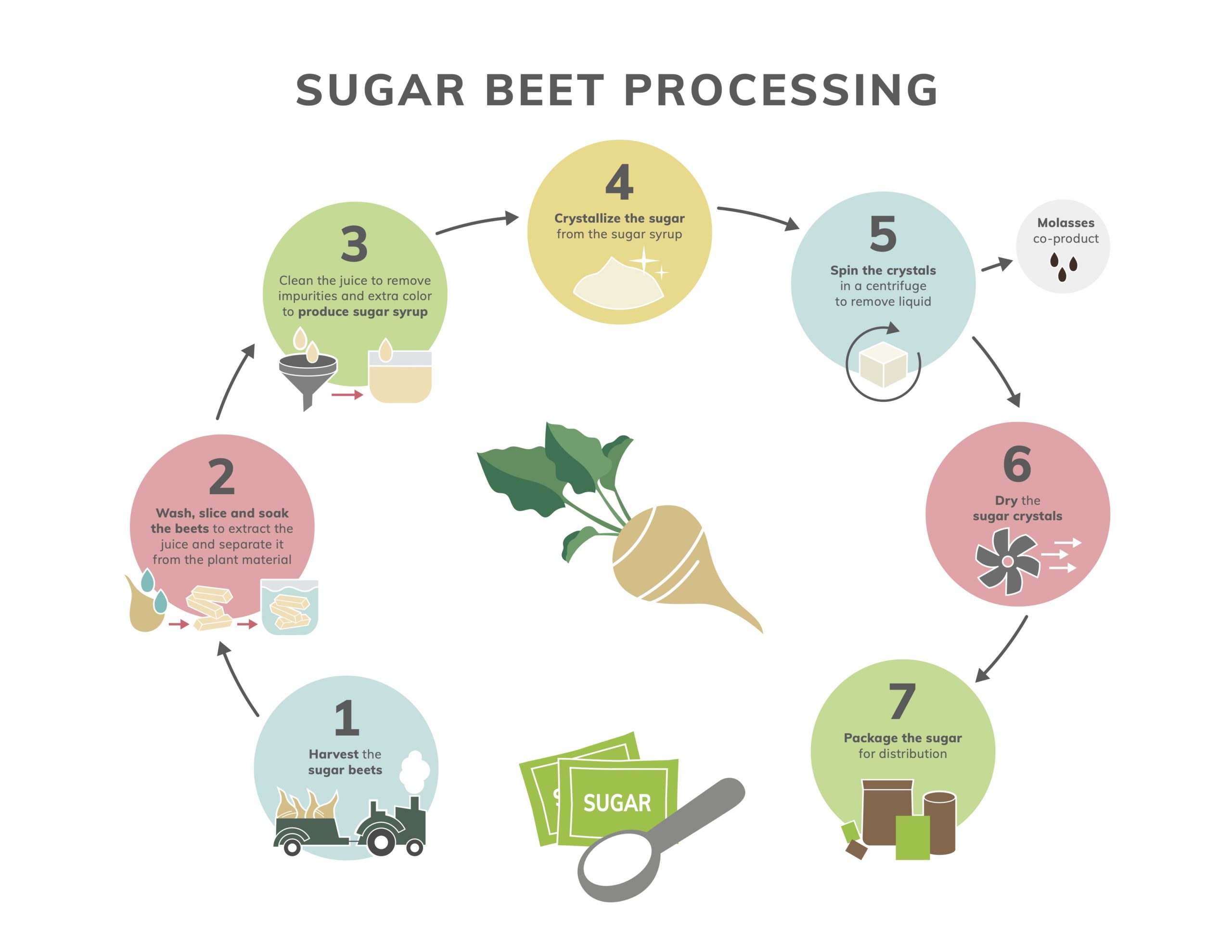
Report this wiki page